Les capteurs IBS et la gestion électrique des véhicules
20 avril 2021
Temps de lecture : 4,1 minutes
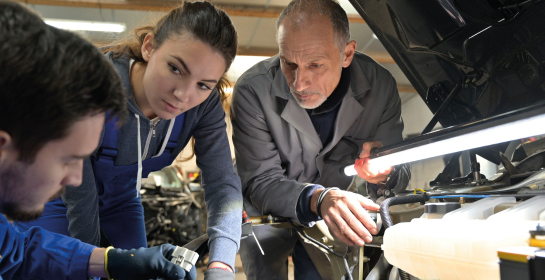
Tout le monde n’a pas forcément conscience du fait que l’expression: « la gestion intelligente de l’énergie du véhicule », de nos jours, regroupe tout un ensemble de dispositifs visant à surveiller, gérer, contrôler et couper l’alimentation électrique des voitures. La gestion de l’alimentation électrique sur les voitures de nouvelle génération doit être contrôlée avec précision. Il en va de la consommation de carburant et directement de la pollution émise par le moteur thermique. Cette gestion doit être correctement prise en charge par des batteries de dernière technologie. En présence d’un véhicule équipé de beaucoup d’options, et possédant un ...
Tout le monde n’a pas forcément conscience du fait que l’expression: « la gestion intelligente de l’énergie du véhicule », de nos jours, regroupe tout un ensemble de dispositifs visant à surveiller, gérer, contrôler et couper l’alimentation électrique des voitures.
La gestion de l’alimentation électrique sur les voitures de nouvelle génération doit être contrôlée avec précision. Il en va de la consommation de carburant et directement de la pollution émise par le moteur thermique. Cette gestion doit être correctement prise en charge par des batteries de dernière technologie.
En présence d’un véhicule équipé de beaucoup d’options, et possédant un système électrique abondant, il est de plus en plus fréquent de trouver des batteries de type « Heavy Duty » ou batterie avec « technologie AGM » (Absorbant Glass Mat = fibre de verre absorbante).
Dans le premier cas, avec la batterie « Heavy Duty », on peut expliquer simplement que c’est une batterie traditionnelle classique, mais où les éléments de matière active (plomb) sont surdimensionnés, afin d’améliorer ses caractéristiques de performance.
Dans le second cas, au contraire, avec l’abréviation « AGM », on se réfère à une batterie caractérisée par une structure interne différente. L’électrolyte liquide de cette batterie est absorbé en totalité par capillarité et donc immobilisé dans des buvards (mat) en fibre de verre, placés entre les électrodes. Cette méthode de fabrication permet de réduire l’espace séparant les plaques positives des plaques négatives, ce qui diminue la résistance interne de la batterie. Il en résulte un gain de place et ainsi la possibilité de mettre encore plus de matière active dans un même volume ce qui augmente la puissance finale de cette batterie.
Il est bon de préciser que, dans le cas des batteries “Heavy Duty” et des batteries “AGM”, nous ne parlons pas d’appellation commerciale des fabricants, mais des types de production, qui sont ensuite adoptées par les différents constructeurs: « la figure 1 » fait référence à une batterie « Heavy Duty” sur Fiat 500 (2009), et une batterie “AGM” sur l’Audi A3 (2012).
Cette petite révolution dans le domaine des batteries automobiles est le résultat, comme on pouvait s’y attendre, des besoins croissants en électricité. Il en résulte une autre conséquence importante: l’utilisation de capteurs électroniques dont la fonction est de surveiller en permanence l’état de charge et de la santé des batteries en question. Ces appareils de mesure sont appelés « IBS » (capteur de batterie intelligent), ou « BMS » (Battery Management System).
L’exemple suivant montre deux capteurs IBS de marque différents: un « Continental » (BMW Série 1, 2009), et un « Magneti Marelli » (groupe Fiat) (figure 2).
Ces capteurs surveillent en permanence la batterie afin d’informer d’un état de batterie faible par exemple. Sur les véhicules avec Start & Stop, il faut interdire l’arrêt automatique du moteur si la batterie ne peut pas supporter une suite de redémarrage automatique du moteur, ou encore, désactiver temporairement certains consommateurs électriques non indispensables au fonctionnement du véhicule: habituellement le confort.
Le capteur « IBS » (1) est fixé et connecté électriquement au pôle négatif de la batterie, et relié à la masse (2). Il est alimenté par un câble (4) à la borne positive de la batterie et une connexion supplémentaire (3) est utilisée par le capteur pour envoyer des données au calculateur moteur ou habitacle. Le capteur utilise une interface de données série bas débit de type LIN.
Le capteur “IBS” sert précisément à détecter l’état de charge de la batterie par la mesure périodique des valeurs de tension et de température de la batterie, le courant de charge et le courant de décharge.
Sur la base de ce qui vient d’être spécifié, il est facilement compréhensible qu’une gestion de l’alimentation de ce type apporte des avantages considérables pour la longévité de la batterie. Mais lorsque la batterie ou le capteur présentent une anomalie, le système peut désactiver certains consommateurs électriques. La lecture des anomalies doit être lue à l’aide d’un outil de diagnostic afin de s’assurer de l’élément défectueux. En cas de remplacement de la batterie ou du capteur IBS, le technicien devra paramétrer le calculateur pour expliquer que des éléments ont été remplacés. Si cette opération n’est pas réalisée, le calculateur ne pourra pas surveiller correctement la batterie, il en résultera un défaut de charge et un risque de non fonctionnement de certains consommateurs électriques.
Articles similaires